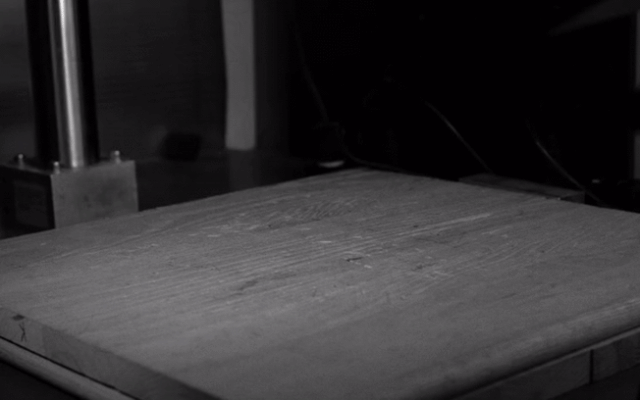
Introduction: Setting the Bar High
In Point-of-Care-Ultrasound, the durability of equipment is paramount. Without quality systems that are ready to use, the immediacy of patient care can be negatively impacted. To ensure reliability and up-time, Sonosite transducers are tested to the limit. This process consists of extensive testing protocols that go beyond industry norms.
Beyond Flexibility: The Sonosite Flex and Twist Test
At Sonosite, we demand more of our transducers. Our testing bends, flexes, and twists transducer cabling over 50,000 cycles to represent typical clinical usage over 5 years. George Myers - Compliance Engineer at FUJIFILM Sonosite states, “We test each transducer in anticipation that they are going to be used in a rugged environment to provide equipment that can endure challenging settings. The goal of the flex and twist test is to simulate the life of the product. We evaluate how exactly the transducer will fit in our customers’ hands – every rotation and movement are accounted for. They are tested with a full range of motion to test how each transducer will be used in the field.” This test helps ensure that our transducers can withstand continual use, even under the most demanding clinical environments.
Disinfectant Compatibility
After establishing the reliability of our cabling, the next step is to test our transducers against a variety of cleaners and disinfectants. This phase ensures that our transducers can withstand regular cleaning protocols without compromising performance.
"We work to prepare our transducers for the expected exposure to cleaning and disinfecting chemicals that occur in the hospital today. We are always learning and working hard to ensure patient safety first and foremost,”
Keith Williams – Signal Path Leader at FUJIFILM Sonosite.
The Immersion Test
Durability against fluid ingress is another imperative factor in becoming a Sonosite transducer. Every Sonosite transducer must pass a rigorous submersion test, where they are submerged in water for thirty minutes. We then test transducers in Saline solution with an electrical charge for safety measures. Our transducers are rated IPX7, which helps ensure that our transducers can endure accidental exposure to fluids, maintaining their functionality and reliability.
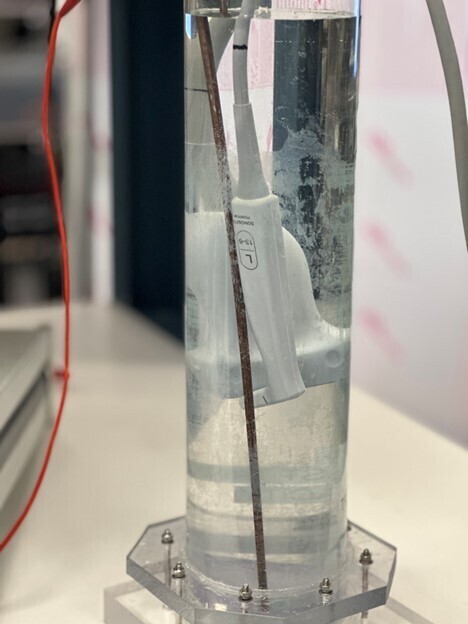
Extreme Conditions: Simulating Harsh Environments
To simulate the challenging conditions that our customers face in diverse clinical settings, we subject our systems and transducers to similar extreme environments. This includes maintaining scanning at 104 degrees Fahrenheit (approximately 40 degrees Celsius) with 95% humidity for 120 hours, followed by a rapid cooldown to 32 (10 or 0 C, excluding T probe) degrees Fahrenheit. (insert link to doctors without borders) This is what enables clinicians all over the world to choose Sonosite for their global health missions.
The Ultimate Test: Drop Testing for Real-World Durability
We drop our transducers because we know that accidents happen. The final hurdle in our testing journey is the Sonosite drop test, a rigorous protocol that is unique to Sonosite in point of care. We begin this by repeating a catastrophic drop test at a height of 1 meter/3 feet that mimics what could happen if a transducer falls off the side of a cart. We then go on to evaluate our transducers for the daily wear and tear of intense clinical use. To do this, we drop transducers at shorter heights (6 inches) over one hundred times to mimic the daily wear and tear of intense clinical use. This step helps ensure that our transducers are not only durable but also resilient and capable of withstanding the rigors of constant use.
The Sonosite Promise of Durability
Not only do we test our transducers to make sure that they’re durable, but we also have a warranty to maximize our customers’ uptime. Our Sonosite standard warranty covers damage to transducers that are accidentally dropped, which is critical to our customers’ peace of mind. The environments that our customers work in can be chaotic – and we understand that. We design, build, test, and warranty our transducers differently with exactly these clinical settings in mind.
Any Patient. Anywhere. Anytime.
“Our jobs are to test our transducers to the limit to ensure that when they leave our doors, they are safe, durable, and ready to use. Furthermore, the biggest goal we have is to ensure quality imaging with our equipment so that the clinicians and their tool can work in tandem accurately and effectively,”
Roger Swezey – Senior Engineering Technician at FUJIFILM Sonosite.
Through a comprehensive series of tests—from flex and twist to extreme condition endurance and drop testing—Sonosite transducers are meticulously engineered to withstand the challenges of clinical environments. We are committed to exceeding industry norms, ensuring healthcare professionals can rely on dependable and high-quality medical imaging solutions.
![]() | ![]() | ![]() |
Please note this article refers to our new transducer fleet, which specifically excludes our T8-3 transducer.